Bendability often plays a significant role in determining which materials a product designer can use in their product. Although bending may seem like a simple processing step, not all materials bend easily.
Bendability, which indicates how easily you can bend a material without breaking it, is commonly associated with aluminum. Purer aluminum alloys, such as those used for household aluminum foil, are highly flexible and exhibit excellent bendability. However, adding other alloying elements to improve strength or other properties can impact bendability.
Do you want to know more about aluminum bending? This article will explain what controls bendability and which alloys are best for bending. So let’s start!
Table of Contents
What Factors Affect Bendability?
Before discussing aluminum alloys, we should cover some background about the factors that affect their bendability. As you can imagine, products like aluminum foil, gutters, traffic signs, and automotive body parts, which are all made from aluminum alloys, have different bendability.
Three factors control the bendability of the various alloys in these products:
- The formability of the aluminum alloy
- Thickness and bend radius
- Percent elongation
Let’s have a deeper look at these factors!
1st Factor – Formability
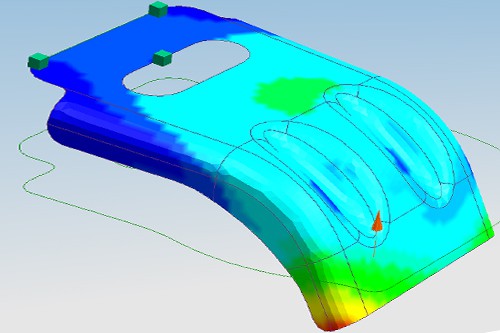
NX One-step Formability Analysis by Siemens PLM Software
Formability is the ability of a given material to experience permanent deformation without the forming process cracking or tearing it. Permanent deformation is also known as plastic deformation in the materials science world.
Generally speaking, formability is a relative term and not a specific value. For example, the applied force necessary to shape a product depends on more than just the strength and ductility of a material. It also depends on factors such as the shape of the part and the thickness of the starting material.
In other words, we can measure the forming force to produce a specific part from a particular starting material. However, changing the shape of the part or the physical properties of the starting material will change the amount of force that needs to be applied.
That said, there are standardized tests, such as the ASTM E2218: Standard Test Method for Determining Forming Limit Curves. We can use these tests to establish a formability “ranking” for different sheets of alloy. We can use them to learn which alloys have better baseline formability.
2nd Factor – Thickness and Bend Radius
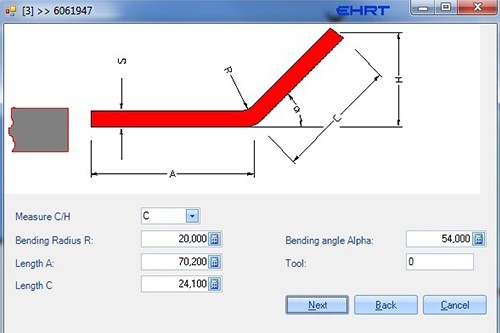
PowerBend Bending Software Parameter EHRT by EHRT Maschinenbau GmbH
If you’ve handled regular aluminum foil, you’ll know that it is effortless to bend. However, if you had to bend a sheet of aluminum that was one-thousand times thicker than aluminum foil, it would be much harder! That is because the thicker a material is, the more difficult it is to bend.
You can also bend an aluminum gutter with your bare hands. But if you try to bend it to a tight angle without breaking it, you will have a hard time! Bending metal to a small bend radius has the potential to cause tearing or cracking.
The Fabricator offers certain key tables and general rules which are helpful for understanding the limits to bendability for specific aluminum alloys. You can use these to determine the minimum allowable bend radius for particular thicknesses of aluminum sheet.
3rd Factor – Percent Elongation
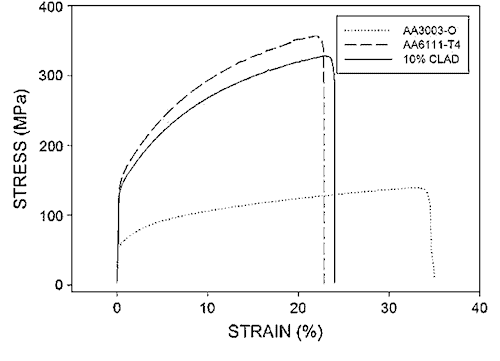
The Deformation of Clad Aluminum Sheet Produced By Direct Chill Casting – Scientific Figure on ResearchGate. [accessed 5 Aug, 2021]
The more ductile aluminum alloys can experience more significant plastic deformation with small increases in applied stress. This results in better overall aluminum bendability.
Like the other properties, the percent elongation varies for each alloy. Take a look at the stress-strain curve above. You’ll see that annealed aluminum alloy 3003 (shown as AA3003-O) has a very high percent elongation (strain %) of roughly 35%. It has very high bendability relative to other alloys.
3 of the Best Aluminum Alloys for Bending
Numerous metal alloying agents can be combined with aluminum to produce different aluminum alloys. The system for naming them uses four digits, with the first digit representing their chemical composition. We explain this in our article on aluminum alloy designations and tempers.
Generally speaking, aluminum alloys from the 1XXX, 3XXX, and 5XXX series demonstrate better bendability than other aluminum alloys. Some 6XXX series alloys are fairly bendable as well.
However, the different properties offered by each may make some more desirable than others. For example, 1XXX series aluminum generally has poor mechanical properties and is not suited to structural applications.
Now let’s discuss which alloys offer the best bendability and when you should use them.
#1 – Aluminum Alloy 3003
This alloy is primarily alloyed with manganese and is one of the most commonly used aluminum alloys for bending applications. It has excellent formability properties and does not require heat to be bent or molded.
Companies often make gutters, roofing, siding, chemical equipment, and storage tanks from 3003 aluminum.
#2 – Aluminum Alloy 5052
With magnesium as the primary alloying element, AA5052 demonstrates moderate-to-high strength characteristics. At the same time, it retains good bendability, and designers can use it for more intensive applications than AA3003. The corrosion resistance of this alloy is also excellent against seawater, meaning it is excellent for applications in marine equipment.
Manufacturers often produce hydraulic tubes, traffic and hardware signs, medical equipment, marine equipment, and electronics (chassis and enclosures).
#3 – Aluminum Alloy 6061
You will find this is an extremely common alloy in your day-to-day life. Even though it is not as bendable or formable as the two alloys above, it is the strongest among all three. It has magnesium and silicon as alloying elements, and you can further enhance its strength with heat treatment.
Alloy 6061 is widely referred to as “structural aluminum” because it is so commonly used in structural (construction) applications. Nevertheless, due to its outstanding properties, it is also used in food and beverage containers, ladders, aircraft and automotive parts, scuba tanks, bicycle frames, and more.
Why Are These 3 Alloys Important?
Despite their different properties, these alloys are excellent examples of bendability in aluminum alloys. They demonstrate that even though some aluminum alloys feature better formability and percent elongation for a given bend radius and thickness, they each serve a unique purpose and a wide variety of applications.
Even with slightly lower bendability, the strength of alloy 6061 makes it one of the most widely used aluminum alloys. In the same way, alloy 3003 has multiple uses in applications that require superior bendability. Meanwhile, alloy 5052 is commonly used thanks to its balance in terms of bendability and strength.
If you want to keep learning more about the applications of aluminum, check out our service pages for aluminum extrusions and quality rolled aluminum.