Extruding aluminum offers the ability to create a wide array of profiles to meet your needs, ranging from simple to complex. While experienced designers can incorporate a variety of features into a single extruded profile, it may not be possible or practical to achieve all that you need with a single extrusion. This is where joining techniques come into play.
When trying to minimize die and tooling costs, create modular designs, or accommodate specific applications, it may make more sense to design two or more smaller extrusion profiles that you can join together later. However, choosing the most cost-effective and efficient joining method can be overwhelming.
This article offers up various options for designing joined or interlocking aluminum extrusions. It also sheds light on how to choose a suitable joining method so you can better adapt your next design.
Table of Contents
Common Joint Types for Aluminum Extrusions
The versatility of extruded aluminum gives designers access to a wide range of joints that they can apply to their products. Whether you need a permanent, semi-permanent, or non-permanent design, there are lots to choose from.
#1 – Flat Joints
These types of joints are distinct from all the other joints in this list as they are simply “butted” up against one another without any special mating surfaces. Whether you assemble them as a butt joint, lap joint, tee joint, or another arrangement, these joints need to be held together by something other than geometry, such as welding or fasteners.
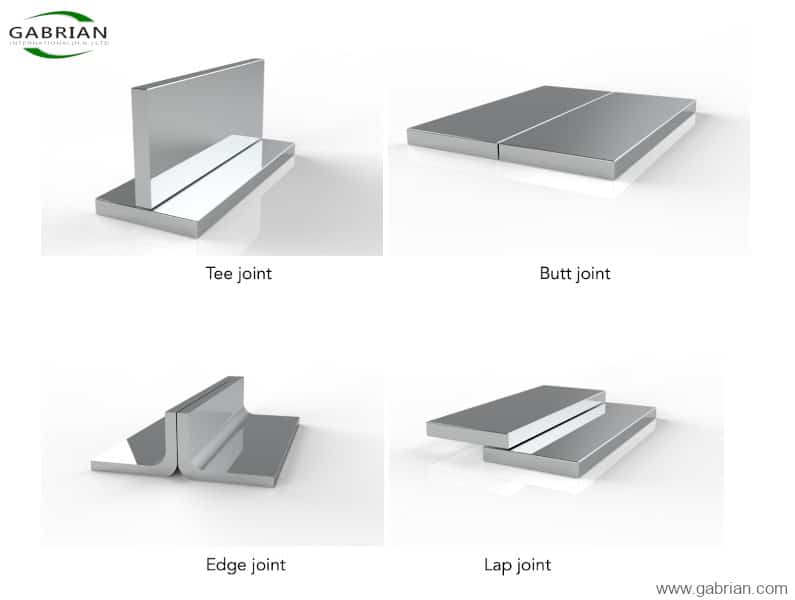
Figure 1: Flat joints
#2 – Nesting Joints
With specially designed mating surfaces, these joints are a bridge between flat joints and more complex mating geometries. Their shape allows for easy, precise alignment between parts, but, depending on the application, they may require more than just geometry to stay together, similar to flat joints. Common examples include tongue and groove joints and half-lap joints, which restrict movement in some directions without locking the components together.
You can make semi-permanent and permanent assemblies from nesting joints using either drilled holes with fasteners such as rivets, or bonding through an adhesive, weld, or other method.
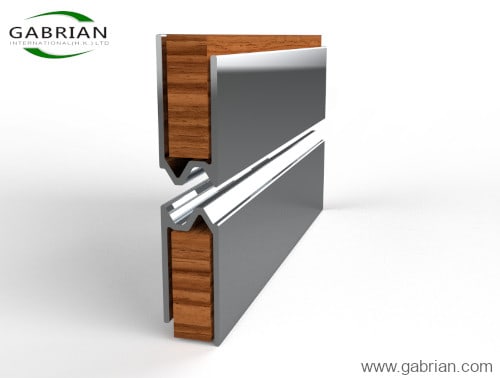
Figure 2: Nesting joint (Tongue and groove joint)
#3 – Interlocking Joints
Interlocking joints are one of the simplest forms of geometry-based joints that don’t rely on fasteners or bonding for joining. Typically made by rotating two components into position, this joint can be sturdy and is quickly taken apart by counter-rotating components out of position. You can add additional elements to lock these joints into position and prevent accidental disassembly, similar to key-locked joints.
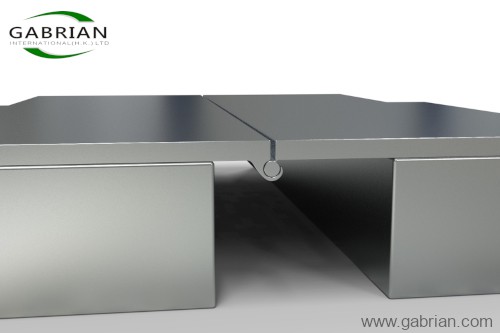
Figure 3: Interlocking joints
#4 – Slip-Fit Joints
Sometimes called sleeve joints, you assemble extrusions using slip-fit joints by sliding them together along their lengths. While this type of geometry-focused joint offers reliable strength, it can be cumbersome to assemble, particularly in small or congested spaces.
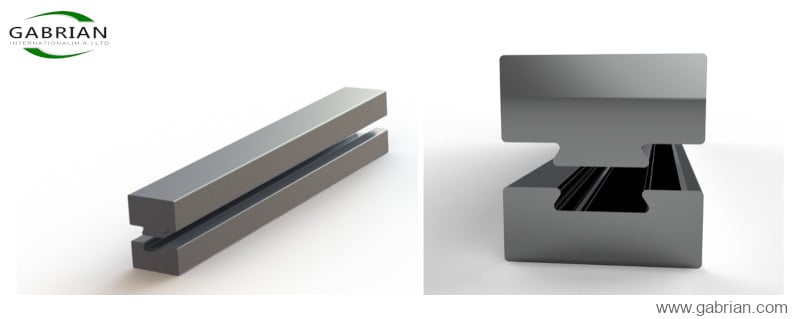
Figure 4: Slip-fit joints
#5 – Snap-Fit Joints
Also known as snap-lock joints, the mating geometries of these joints are generally reserved for more permanent applications. By relying on aluminum’s relatively high ductility to bend without experiencing permanent deformation, snap-fit joints slide together into a locked position that is generally very difficult to take apart.
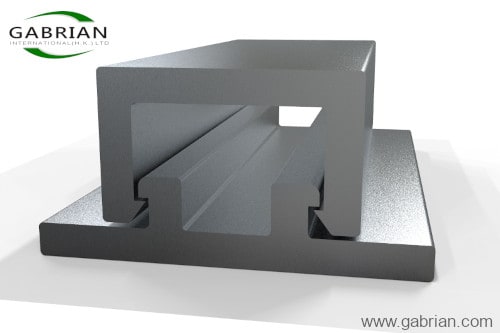
Figure 5: Snap-fit joints
#6 – Nut Tracks
Unlike interlocking, slip-fit, and snap-fit joints, nut tracks rely on more than just geometry for sticking together. Extrusions with nut tracks include a channel designed to accommodate a hex-head nut or bolt so that you can fasten extrusions and other components together as needed. This design is highly modular and customizable, allowing for rapid assembly of custom frames and easy attachment of other add-ons.
T-slot and V-slot aluminum extrusions work similarly to nut tracks but require custom hardware based on their respective building standards.
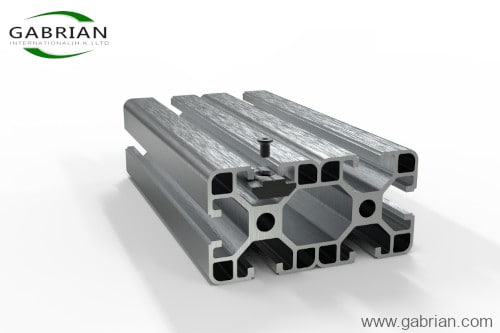
Figure 6: Nut tracks
#7 – Screw Ports
Whether you are adding a protective cover to the end of an extruded segment or affixing a perpendicular component, you may want to consider adding screw ports. Adding a screw boss to an extruded profile is a simple, sturdy way to facilitate adding components to the end of your extrusion.
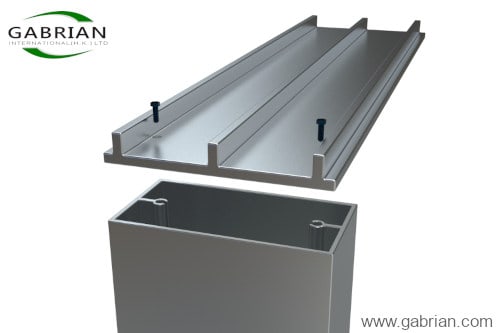
Figure 7: Screw ports
#8 – End Joints
End joints are similar to joints that take advantage of screw ports, adding special channels that allow you to create joints at the ends of extrusions. Unlike screw ports, which allow for the attachment of other components to the extrusion, end-joints let you seamlessly connect extrusions end-to-end. By using an insert such as a coupling or cleat, end joints can either extend extrusions in the same direction or create sturdy corner joints.
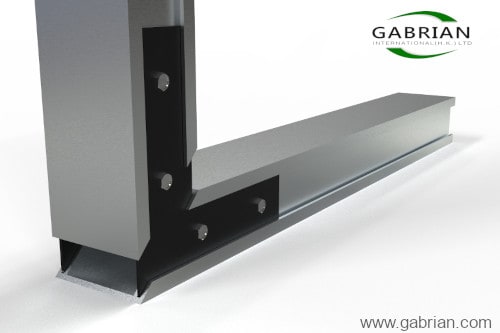
Figure 8: End joints
#9 – Hinge Joints
Whether permanent or non-permanent, most of the joints on this list are designed for fixed applications. Hinge joints are the exception. They are meant to allow for limited rotational movement while still keeping the extrusions aligned.
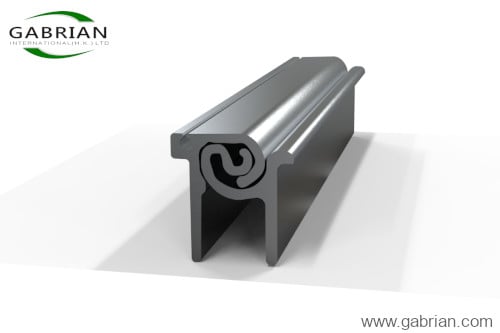
Figure 9: Hinge Joints
#10 – Key-Locked Joints
Key-locked joints are geometry-based extrusions that take advantage of two or more primary extrusions alongside a key to create a stable joint. While the primary extrusions will not lock together on their own, the addition of a key prevents them from coming apart. You must insert the key laterally similar to slip-fit joints, but depending on the application, it may not need to run the length of the entire extrusion.
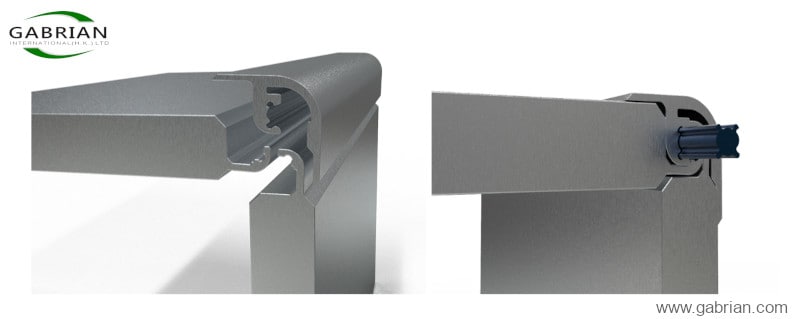
Figure 10: Key-locked joints
Bonus – Combination Joints
While not necessarily a joint on its own, capable extrusion designers can take advantage of multiple joint types to create combination joints. Depending on the intended application for the product, combination joints can increase versatility and improve stability. For example, incorporating a hinge joint into an extrusion profile with a nut track would allow you to firmly attach components along the nut track while allowing rotation around the hinge axis.
How do You Choose the Right Joining Method?
Part of the reason aluminum extrusions are so popular is their versatility, which comes in part from the wide range of joining methods designers can choose from. However, choosing the best one for your application can be challenging.
To simplify this, you should think about the expected applications of your design. Does your design need to be disassembled and reassembled? Is easy field assembly necessary? What tools does the end-user have access to when assembling your products?
Joining Extrusions Permanently
You can use welding, brazing, soldering, and adhesives to combine different extruded profiles permanently. These techniques can be applied either at the time of manufacturing or in the field during the final installation. However, once you use these methods, it is generally difficult to separate the components and reuse them for the same application.
Joining Methods That Offer Customizability
Mechanical fasteners such as nuts, bolts, screws, and rivets offer a higher degree of versatility when joining aluminum extrusions and can often be taken apart and reassembled as needed. Mechanical fasteners offer customizability, making extrusions that use them the first choice for many customers.
Extrusions With Mating Geometries
While you can apply these joining methods to a wide range of manufactured products, one method that is particularly well-suited to aluminum extrusions comes from mating geometries. When the profiles of two or more extrusions fit together, designers can create non-permanent, semi-permanent, or permanent assemblies to match the design application.
Similar to how seasoned woodworkers can create a whole array of sturdy joints depending on their needs, extrusion designers rely on several joint types to create a design that best fits the intended application of their product.
Which Joint Type is the Best?
Unfortunately, there is not a one-size-fits-all solution to joining aluminum extrusions.
Each joining method and joint type has advantages and limitations that make it better suited to specific applications.
For example, suppose you want to create a highly modular assembly capable of integrating a wide range of add-ons. In that case, you’ll most likely want to consider joints that take advantage of fasteners and mating geometries.
However, this type of non-permanent design would not be suitable if you were concerned about thefts or tampering. Instead, you might prefer a permanent or semi-permanent solution that prevents easy disassembly, such as welding or snap-fit joints.
Gabrian offers a full range of Custom Aluminum Extrusion services so that we can manufacture the perfect extruded aluminum product for your needs. Learn more about the design of aluminum extrusions by consulting our Extrusion Design Guide or contacting our service experts.