If you’ve decided to make your products from aluminum and are exploring manufacturing options, you may be trying to determine which processing or forming method to use. Two major contenders are die casting and extrusion, but what is the difference between cast aluminum and extruded aluminum? Before we compare them, we first need to define what each process entails.
What is Die Casting?
Die cast aluminum products are made by melting aluminum ingots, injecting the molten metal into a die mold using a power cylinder or piston, and then letting the aluminum solidify into the die mold’s shape as it cools. While the process is somewhat more complex in practice — including steps like adding alloying elements and deburring — the general principle is relatively straightforward.
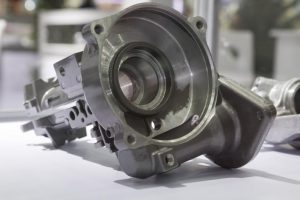
Die castings can be done in a wide range of sizes and can accommodate complex geometries — like automotive engine blocks, for example. After creating a tool steel die mold, you can cast the product numerous times before the mold deteriorates and you need to replace it.
The number of times you can reuse a mold depends on the shape of the part, the allowable tolerances for the end product, and processing conditions. For more information, please view our What is Aluminum Die Casting? article.
What is Extruding?
Extruded aluminum products are made by forcing a heated aluminum billet through a die to produce the desired cross-section. The extrusion can then be cut to an appropriate length and subjected to further processing — like machining bolt holes or fitting together different parts for the final product.
We have provided a complete description of the aluminum extrusion process in our article What is Aluminum Extrusion? The Process in 10 Steps.
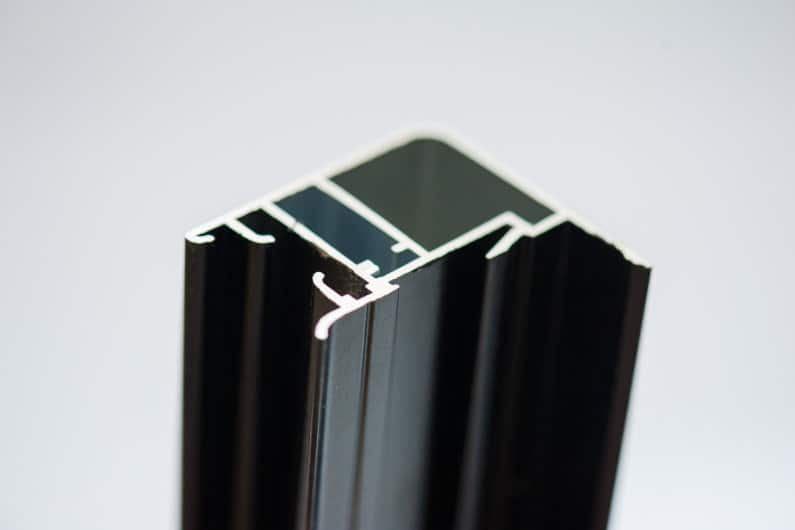
Aluminum extrusions are well-suited to high production outputs, where they rapidly produce reliable, high-strength aluminum products as a result of the work-hardening that occurs during forming.
Which Process is Better for Your Project?
Both die casting and aluminum extrusion have excellent advantages and a few disadvantages that make them better suited for certain applications. To help you decide which process is best for you, take a look at the side-by-side comparison below:
Die Casting
- Makes more complex shapes than extrusions.
- Can make larger finished products than extrusions.
- Generally not as strong as extruded products. There is also the potential for porosity if air gets trapped in the mold.
- Have a rough surface finish and can show seams or other imperfections.
- Die molds are costly and time-consuming to make. They also generally do not last as long as extrusion dies.
- Process changes are time consuming and costly, taking several weeks to prepare a new die mold.
- Typically a more expensive process, die casting is generally used in higher production runs to offset the initial costs.
Extrusion
- Can make a wide variety of shapes but must have a consistent cross-section.
- Size is limited by the size of the aluminum billet.
- The work hardening that occurs during forming strengthens the end product.
- Typically have a very smooth surface finish.
- Extrusion dies are less costly than die casting molds, and new profiles can be manufactured with relative ease.
- A highly adaptable process with relatively little effort or notice needed to make changes.
- Generally a less expensive process. The lower setup cost also makes it more suited to short production runs.
Conclusion
Both die casting and extrusion can be excellent methods for making your aluminum products.
Die castings are generally more costly upfront, but depending on the parts being manufactured, you could save money on post-casting machining and assembly costs. Extrusions can be limiting in terms of shape-possibilities and may require additional post-forming machining and assembly. However, they are generally stronger and less expensive to produce.
The choice you make ultimately depends on the specifics of your project, as you can expect different mechanical properties and manufacturing costs with each processing method.
Learn more about:
➔ The Aluminum Extrusion Process