Reliable Aluminum Extrusion Suppliers in Asia
Work With Manufacturers in India and Our Helpful US-Based Service TeamMinimum Order Quantity: 1000 kg (1.1 US Tons) per shape
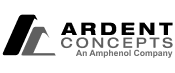
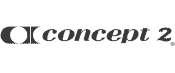
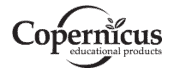
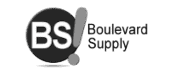
High-Quality Aluminum Extrusions
Elevate your projects with well-made aluminum profiles. We’ve partnered with reliable suppliers in Asia and provide on-the-ground quality control support to ensure you receive top-tier, custom solutions that align seamlessly with your design goals. We turn your ideas into high-quality reality.
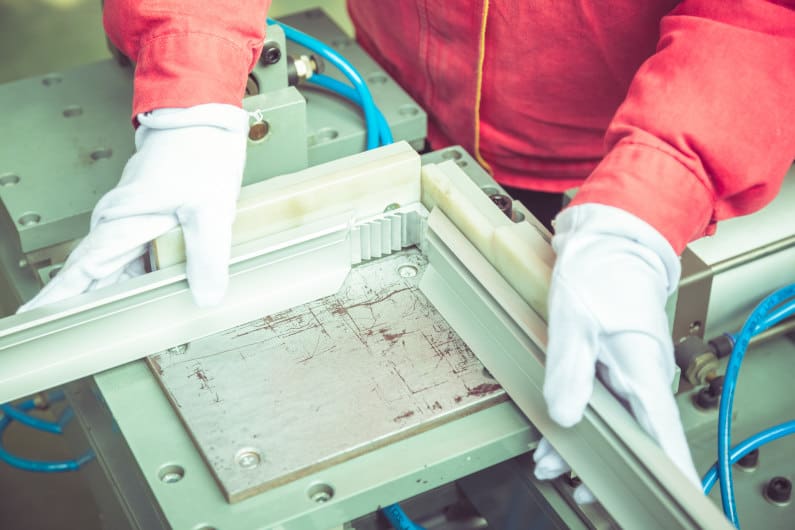
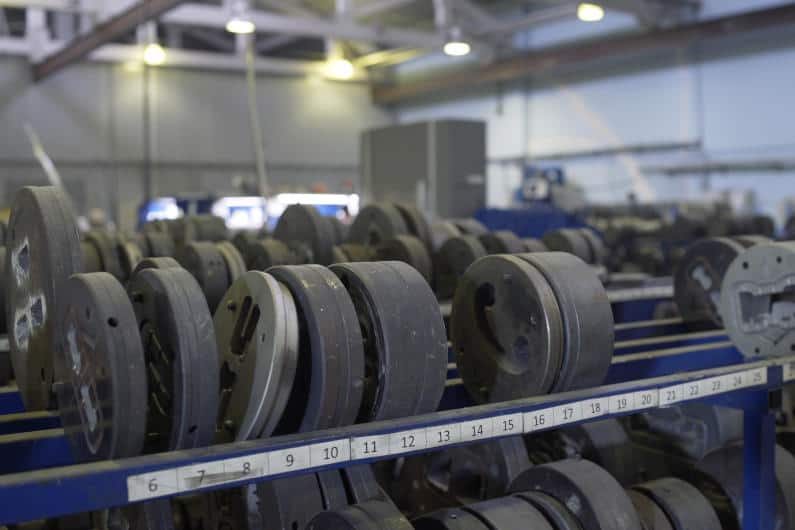
Gain Access to Vetted Extruders in Asia
Unlock the potential of offshore manufacturing with our rigorously screened suppliers in India. During the last 25+ years we’ve developed a reliable network of manufacturing partners. Our team is your on-the-ground presence at the facilities to help ensure quality, manage timelines, and enhance cross-cultural communication.
A Top-Notch US-Based Team
Experience the advantage of clear communication with our global team. Our US- and Asia-based experts are readily available to address your concerns and provide timely updates. From refining specifications to coordinating project details, we streamline collaboration, making your journey from concept to production seamless and efficient.
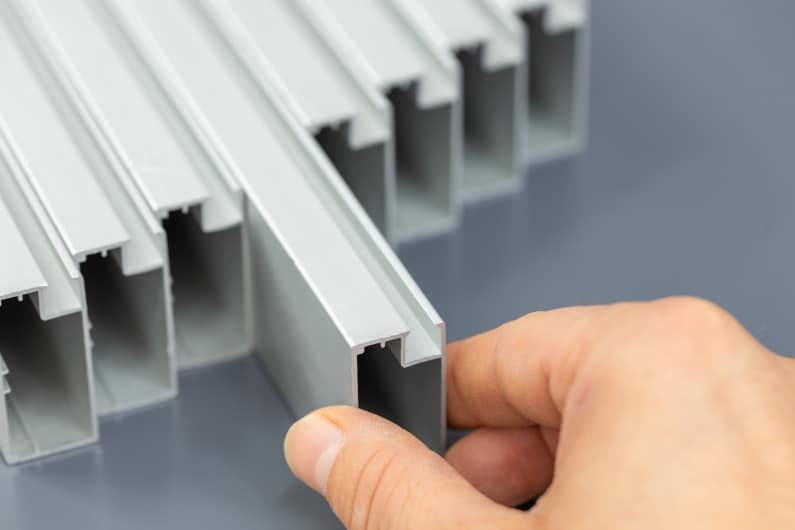
What Our Customers Say:
Aluminum Extrusions for Diverse Industries
Do you need aluminum extrusions tailored for your industry? Whether you’re in machinery, electronics, renewables, or something else, our expertise ensures precision-crafted solutions. Elevate your projects with extrusions that meet the highest industry standards, providing the strength and innovation your applications demand. Gabrian International is your partner in Progress.
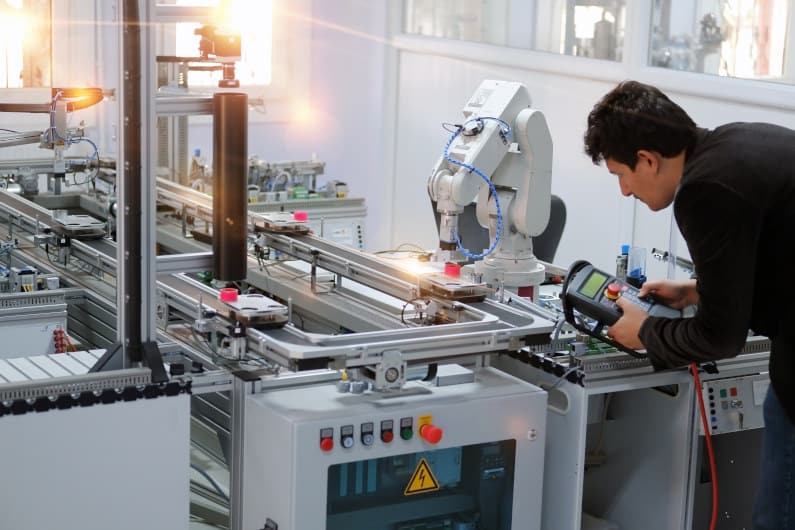
Machinery
Strong and lightweight profiles to ensure the longevity of your machines.
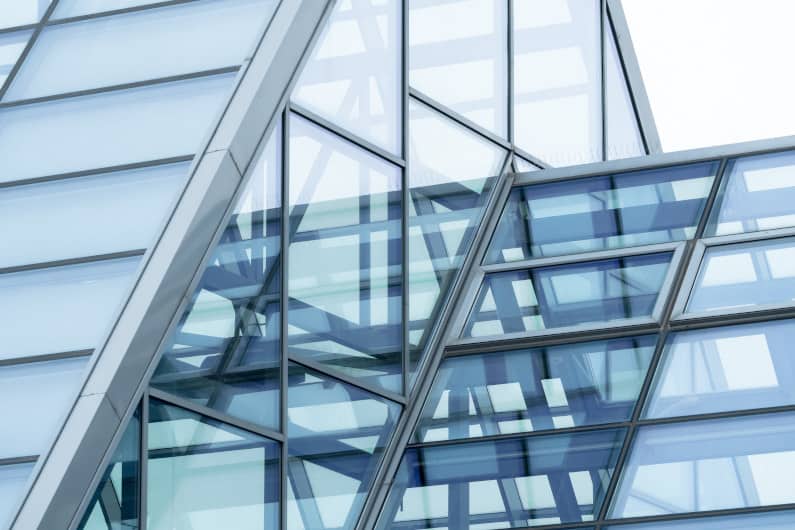
Architectural
Ensure the structural integrity, aesthetics, and sustainability of building projects.
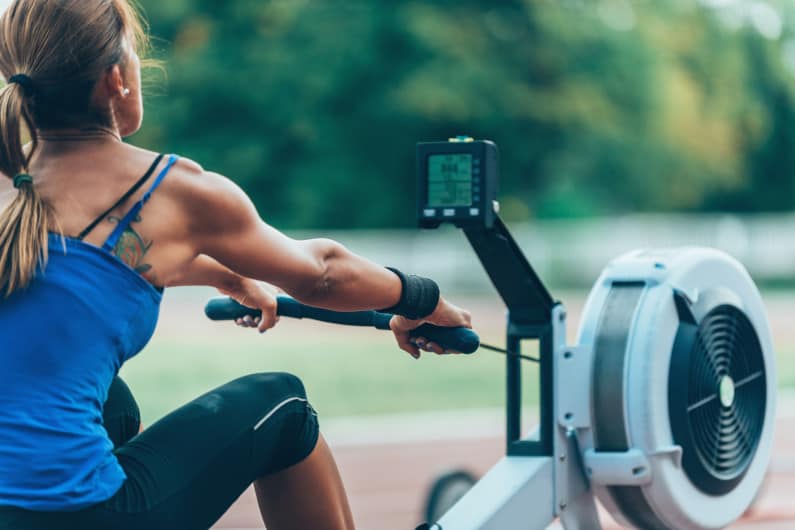
Sporting Goods
Lightweight, durable extrusions ideal for your high-end sporting equipment.
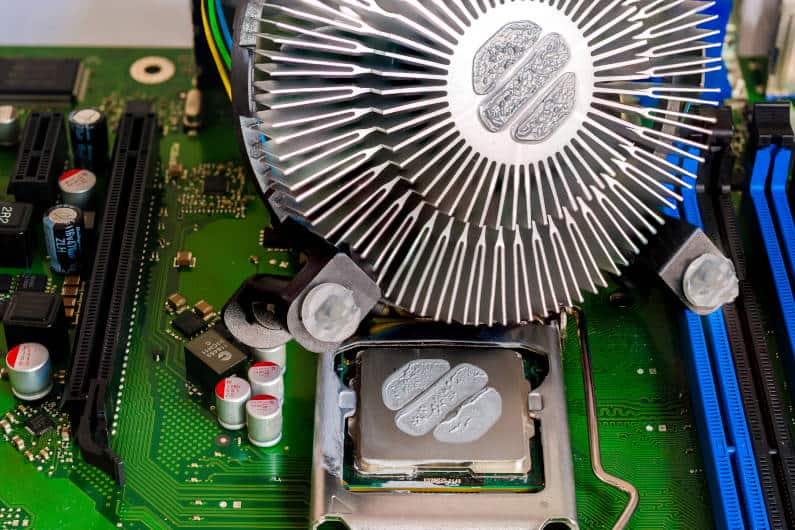
Electronics
Cost-effective, heat-resistant solutions to enhance the performance of your electronics.
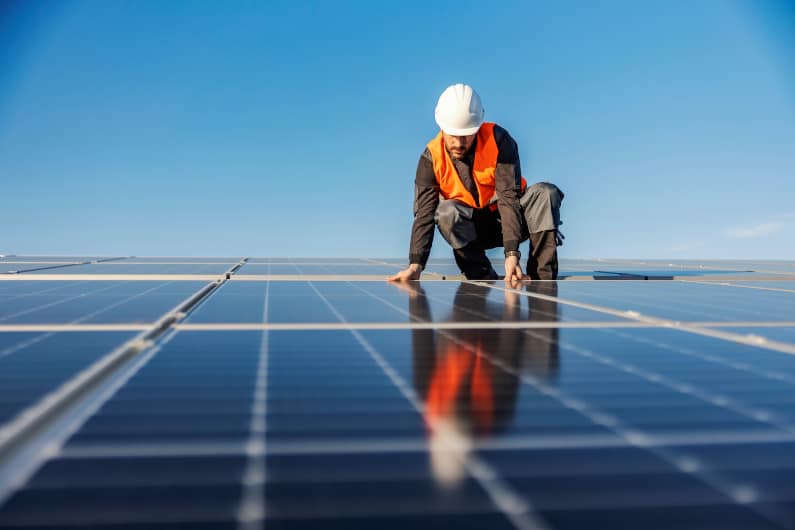
Renewables
Enhance the efficiency and longevity of your green energy solutions.
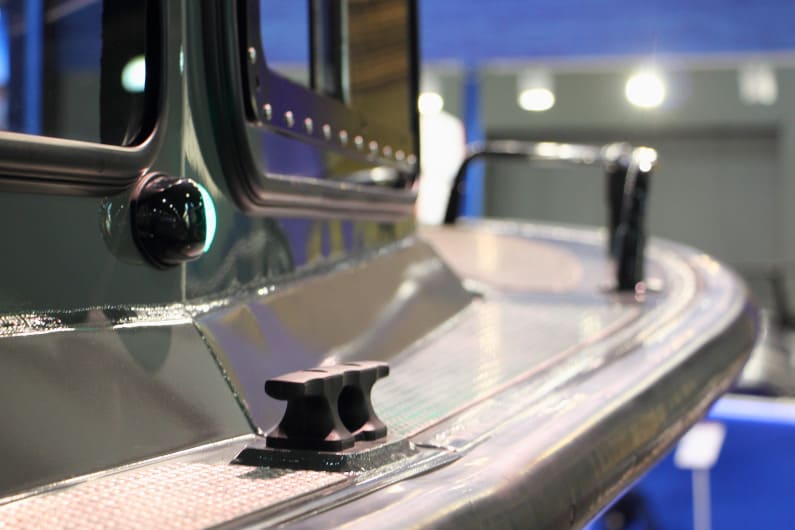
Maritime
Durable and corrosion-resistant profiles to ensure safety and reliability on the water.
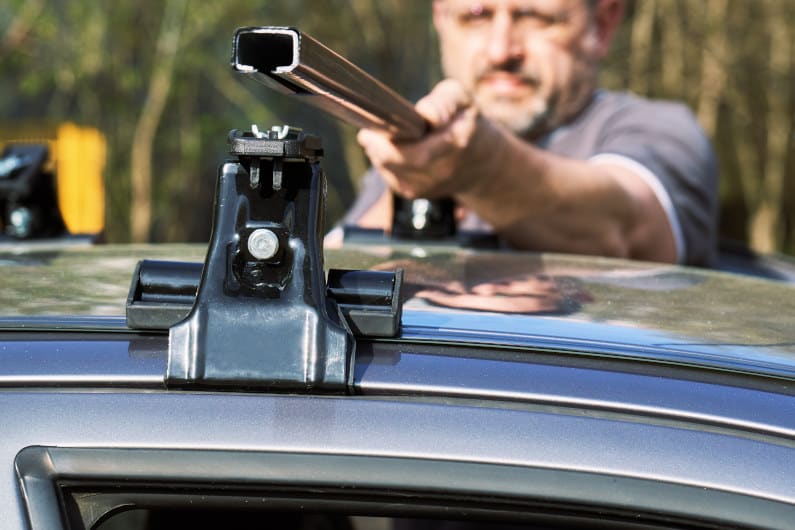
Automotive
Improve vehicle performance, fuel efficiency, and design aesthetics with aluminum extrusions.
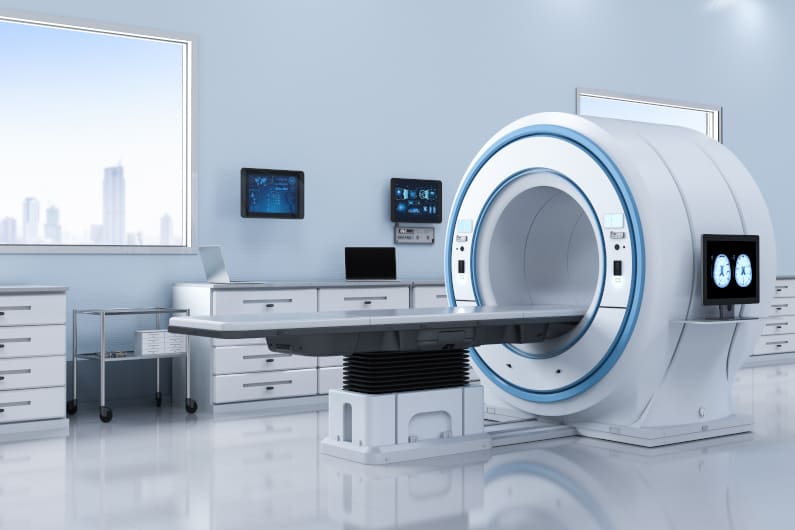
Medical
Precision-crafted components ensure reliability, safety, and innovation.
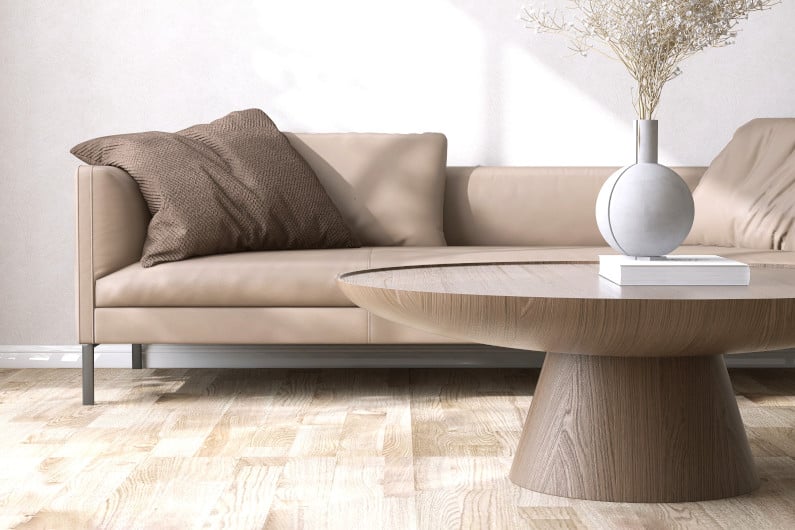
Furniture
Lightweight, durable materials add sophistication and longevity to your furniture creations.
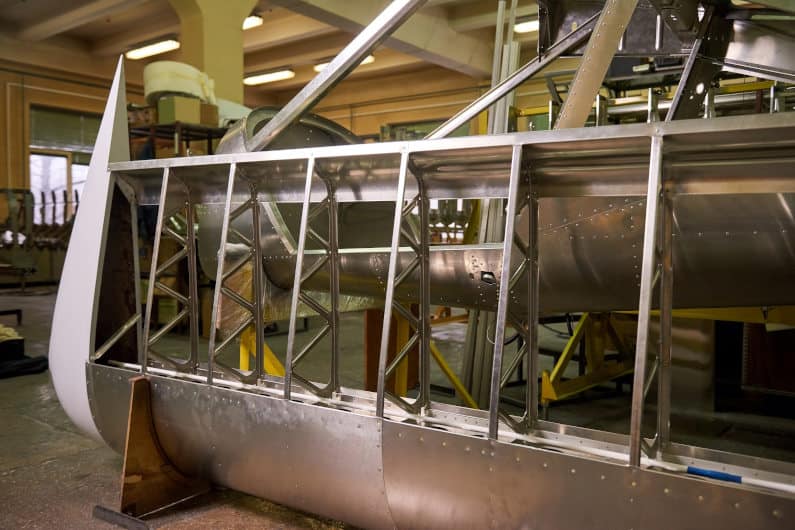
Aerospace
High-strength, lightweight materials to elevate performance and fuel efficiency in the skies.
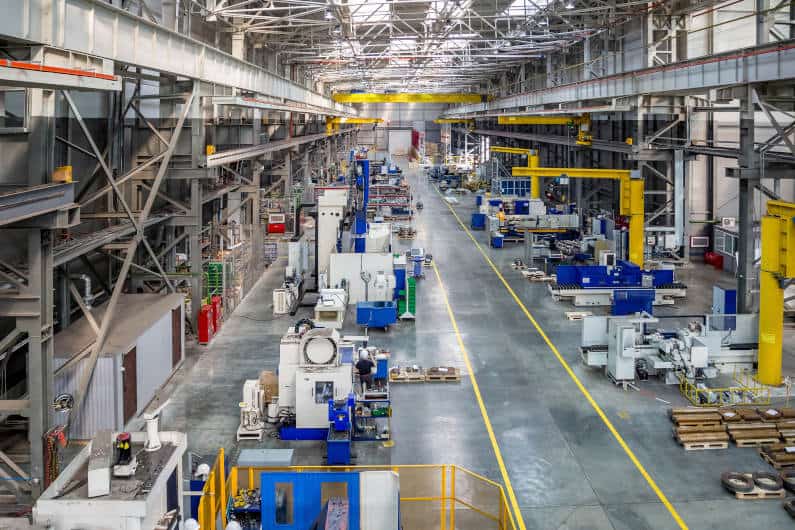
Other Industries
Our aluminum profiles have an endless number of applications in many industries.
Custom or Standard Profiles to Make Your Product a Reality
Whether you have a custom design or would like to take advantage of a catalog with thousands of stock dies, we’ve got you covered.
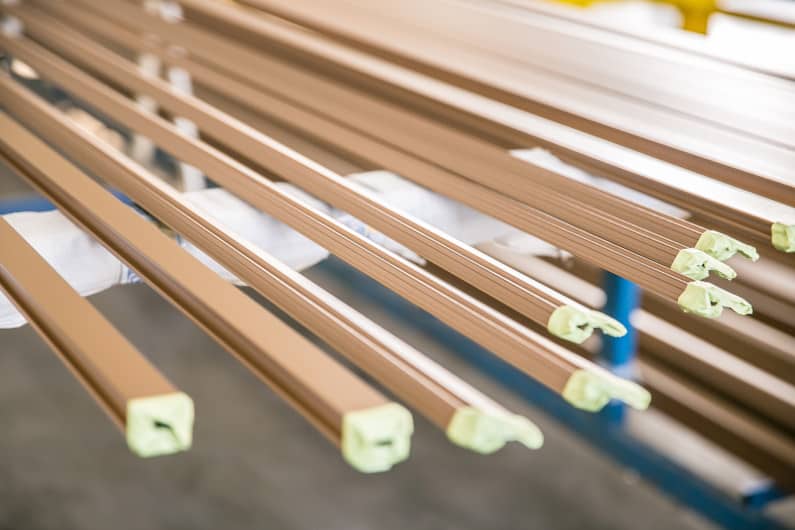
Custom Aluminum Extrusions
Unlock the power of tailored design with our custom aluminum extrusion services. Our manufacturers will create custom dies and tooling based on your unique profile drawings. Your extrusions can then be anodized, powder coated, or receive other finishing. They can also be drilled, cut, post-machined, stamped, bent or undergo other secondary operations.
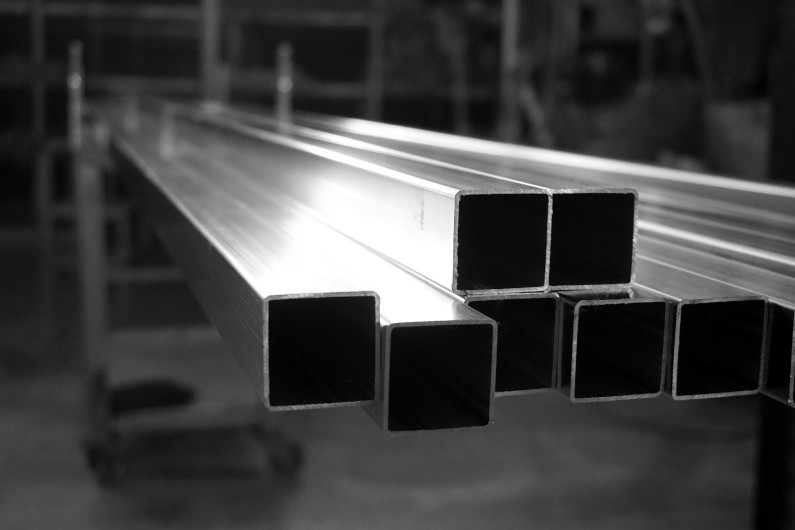
Standard Aluminum Extrusions
Extrusion shapes like channels, angles, and tubes can play a crucial role when you’re building indoor or outdoor structures. Standard architectural trim profiles can enhance the look of your project. We offer all manner of standard profiles in a range of different alloys and can perform secondary operations to make them perfect.
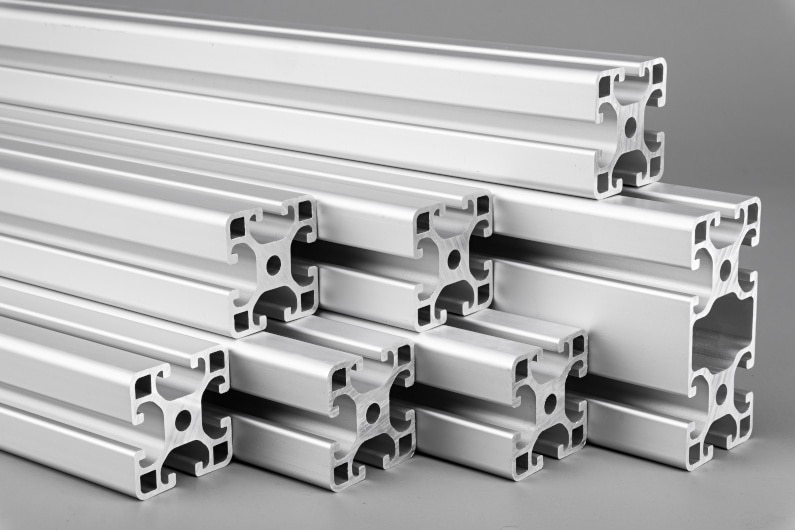
T-Slot Extrusions
Complete large projects using modular t-slot aluminum extrusions. Create the structures you need in your workshop, without any welding required. Using a series of accessories such as bolts and fasteners, you can quickly and easily build machine guards, workstations, shelves, carts, enclosures and more.
Capabilities
We offer extrusions in a wide range of alloys and tempers to meet your needs for strength, machinability, and other characteristics. With a minimum order quantity of 1000 kg (1.1 US tons), we can extrude your custom or standard profiles and perform the secondary operations you require.
Attribute | Options Available |
---|---|
Alloys | 1050, 1070, 1350, 2014, 3003, 3103, 5052, 5054, 5083, 5086, 6060, 6061, 6063, 6005, 6026, 6066, 6082, 6101, 6106, 6261, 6262, 6351 |
Tempers | M, O, T4, T5, T52, T6, T66, T6511 |
Finishing Services | Sandblasting, Anodizing, Powder Coating, Sublimation (Wood Look), PVDF Coating |
Other Secondary | Post-Machining, Cutting, Stamping, Drilling, Welding, Bending, Assemblies, etc. |
Profile Width | Up to 400mm depending on shape, size, and CCD |
Get in Touch With Our Global Team
Contact our team today to tell us about your projects and we’ll help transform your ideas into reality with our reliable and high-quality offshore aluminum extrusion services.
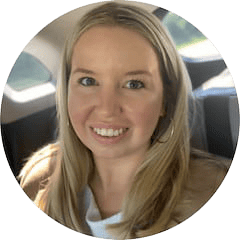
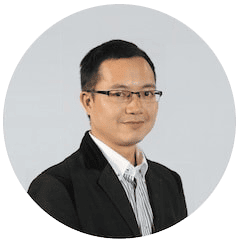
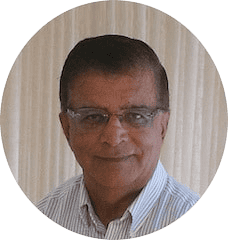
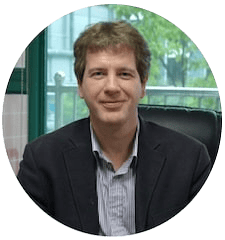
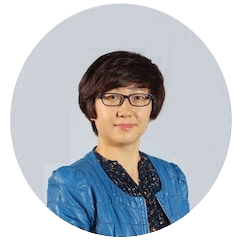
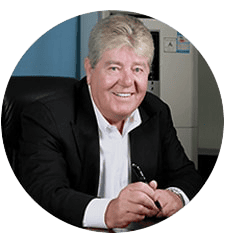