Aluminum alloys are among the top materials used in the construction, aerospace, sports equipment, electrical, and automotive industries. Their excellent strength-to-weight ratio, high relative strength, corrosion resistance, and machinability make them an attractive choice.
Given the wide range of aluminum alloys available, it can be challenging to choose the right one for your project. This article compares two common alloys, 6061 and 7075, and will help you decide between them.
Table of Contents
Alloy 6061 in Review
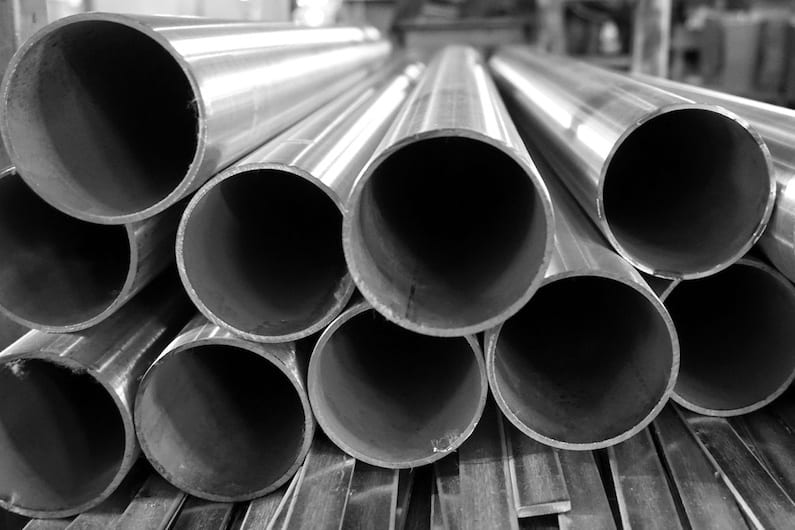
A member of the 6000 series, 6061 aluminum’s main alloying elements are magnesium and silicon, and it’s a great example of a jack of all trades. The alloy is somewhat universal, seeing some exposure in structural and building products as well as the aerospace and recreation industries.
Alloy 6061 displays good tensile strength, which can be improved by temper treatment, and good corrosion resistance, weldability, and workability. Its workability makes it the right choice for many extrusion projects, as it is easy to form.
The alloy is widely available at a relatively low cost and is a great option to produce varied and precise components in different shapes. Although alloy 6061 doesn’t rank first in any aluminum properties tier list, it’s a great and reliable all-around aluminum alloy to work with.
Alloy 7075 in Review
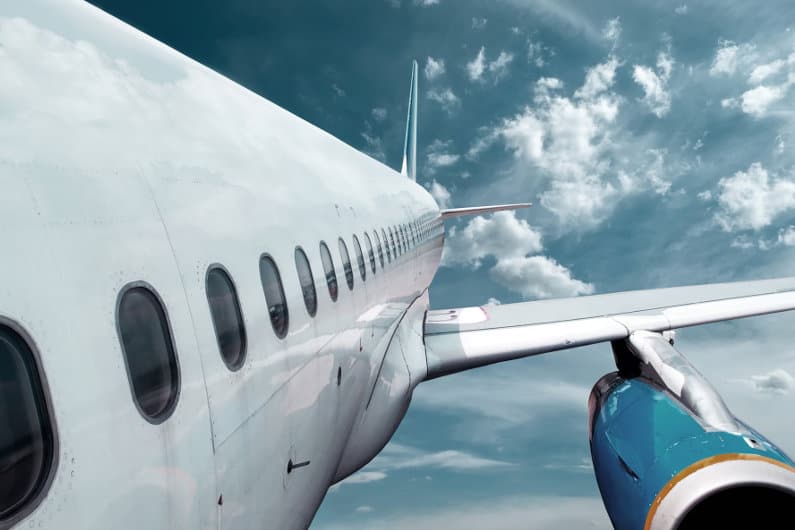
Aluminum 7075 is a member of the 7000 series, which has zinc as its main alloying component and is well known for its extraordinarily high strength. Tempering treatment can then further enhance its high mechanical strength. This property makes alloy 7075 very popular in the aerospace and defense industries.
Its strength is comparable to that of many types of steel, but it has a much lower density. The alloy is an excellent substitute to steel in high-stress applications. It also excels in withstanding fatigue stress, rendering it very reliable, a quality much sought after in the industries mentioned above.
Alloy 7075 offers only average corrosion resistance, an outcome of the small amount of copper included in its chemical composition. It also features reasonable machinability and poor forming and weldability. Another drawback of this alloy is that it has a comparatively high cost relative to other aluminum alloys due to its exceptionally high strength.
6061 vs. 7075 Aluminum Alloys Comparison
The following table provides a direct comparison between these two aluminum alloys, highlighting their respective strengths and weaknesses. What are the differences between 6061 and 7075 aluminum?
Alloy 6061 | Alloy 7075 |
---|---|
• Aluminum alloyed with silicon and magnesium. | • Aluminum alloyed mainly with zinc, with small amounts of magnesium and copper. |
• Structural grade aluminum alloy | • Structural grade aluminum alloy |
• Medium strength, can be high with temper treatment. | • High strength, and even higher with temper treatment. |
• High strength to weight ratio, with low density. | • Very high strength to weight ratio, even considering a somewhat higher density compared to 6061. |
• Good corrosion resistance. | • Average corrosion resistance. |
• Good weldability, workability, and machinability. Great for CNC machining and extrusion projects. | • Regular machinability, and poor weldability and workability. |
• Very high versatility, used in many industries. | • High-strength applications, mainly in the aerospace industry. |
Applications for the 6061 and 7075 Aluminum Alloys
Below are some typical applications for each of these alloys. It is worth considering the situations in which engineers commonly use each alloy to get a better idea of which one might be more appropriate for a given project.
6061 Aluminum Alloy | 7075 Aluminum Alloy |
---|---|
Building products | Aircraft wings and fuselages |
Electrical products | Missile parts |
Piping | Gears and shafts |
Bicycle frames | Worm gears |
Furniture | Regulating valves |
Automotive parts | Fuse parts |
Should You Choose Aluminum Alloy 6061 or 7075?
As with most things, it depends. Both alloys exhibit high strength-to-weight ratios and would be good options for non-intensive, general purposes. Nevertheless, each of them excels in particular uses, and it comes down to the intended use and budget.
Aluminum 6061 would be a better choice when the product will be welded or formed, requires moderate to high tensile strength, or corrosion is a concern. It is also a better option for extruding complex shapes or when your budget is limited.
Aluminum 7075’s very high strength is its main characteristic. Therefore it would be more appropriate when an extraordinarily high tensile strength is required, accompanied by a high strength to weight ratio and high fatigue resistance.
To learn more about selecting the right alloy and designing for manufacturability, you can refer to our aluminum extrusion design guide.