Aluminum and its alloys are extremely popular for a wide range of applications. Nevertheless, there is a common misconception that aluminum cannot be effectively joined through normal welding processes the way steel alloys can.
Many people think they have no choice but to join aluminum pieces with mechanical fasteners, like rivets — but the truth is more complex. There are some nuances when it comes to welding aluminum.
In this article, you’ll get a general overview of just how weldable aluminum and its alloys are. You’ll also learn about welding methods and the six best aluminum alloys for welding. This information will help you determine whether you can weld your aluminum product.
Table of Contents
How Weldable is Aluminum?
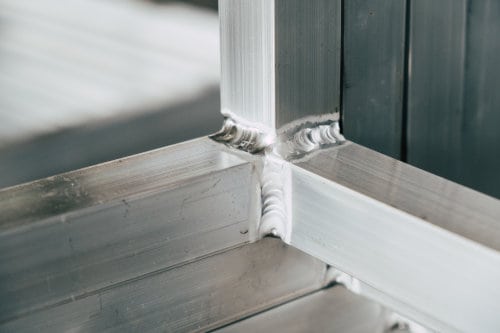
Square aluminum profiles welded into a frame
Generally speaking, aluminum’s capacity to be welded (weldability) varies between different alloy series. It can range from “very good” to “unweldable by common arc welding methods.” That said, most aluminum alloys can be welded under the right conditions and by taking proper precautions.
Due to its physical and chemical properties, the techniques for welding aluminum are different from other metals. As such, only professionals who are specifically trained for aluminum welding should perform this practice.
Two properties, in particular, make welding aluminum tricky.
- The oxide layer on its surface
- Aluminum’s thermal conductivity
Let’s talk about each of these properties.
The Oxide Layer
One of the precautions welders need to take with aluminum is to prepare, or clean, the surface they are going to weld. Aluminum naturally forms a layer of oxide on its surface, which causes issues.
This oxide layer is corrosion-resistant — a desirable feature most of the time — but the material is hard. It has a melting point nearly three times that of aluminum. So if the aluminum oxide is not thoroughly removed, it can create impurities in the joint, leading to porosity and fractures.
Thermal Conductivity
Another thing to keep in mind is that aluminum has a much higher thermal conductivity than steel. And although its melting point is lower than steel’s, you need to apply more heat energy to the weld.
One way to help combat this high thermal conductivity in some joints is to preheat the aluminum. Experienced welders do this to prevent burn-through on thinner aluminum portions and, for thicker materials, to ensure sufficient weld penetration.
Methods for Welding Aluminum
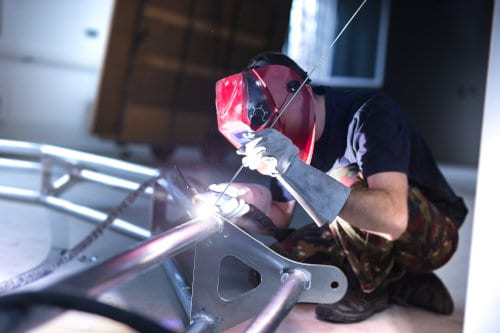
Man using a TIG welder to construct an aluminum frame
The best method for welding a specific aluminum project will depend on various factors. These can include the material’s thickness, the part’s purpose, and the alloys being welded, among others.
Generally speaking, the two most common welding methods for aluminum are Metal Inert Gas (MIG) welding and Tungsten Inert Gas (TIG) welding. For these procedures, a trained specialist needs to select the appropriate filler metal composition. They will take a variety of factors into account, such as:
- The weldability of the parent metal
- Requirements on mechanical properties
- Corrosion resistance
- Anodizing coatings
Tables exist to help select the appropriate filler metals for many aluminum alloys.
Friction Stir Welding (FSW) is another type of welding that can be used for some applications to create very high strength welds. Unlike the arc welding methods we’ve mentioned, it involves using a high-speed rotating cylindrical tool to soften and mix aluminum together.
Unfortunately, FSW may not be suitable for all circumstances, as it requires a specialized equipment setup and is only capable of welding butt joints.
Several other welding methods can be used for welding aluminum, such as Laser Beam Welding (LBW). However, these are less common in most industries.
The Weldability of Different Alloy Series
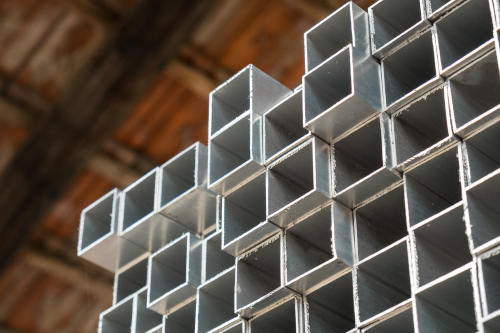
Square extruded aluminum tubes
Although the weldability of different aluminum alloys varies, you can definitely see patterns in their weldability, which varies according to their main alloying elements, or grade series.
Alloys from the 2XXX and 7XXX series are very high strength, often used in aerospace and aircraft applications. But these alloys are sometimes referred to as ‘unweldable.’
Most alloys from these series are extremely prone to hot cracking due to their copper or zinc content. However, the term “unweldable” is misleading, as several of these alloys can indeed be welded. But the welder must put special precautions in place to ensure good weld quality.
Alloys belonging to the 6XXX series have good weldability if proper techniques are employed to combat their susceptibility to cracking. They are not as strong as 2XXX and 7XXX alloys, but they have other excellent physical properties. Alloys from the 6XXX series are often used in welding applications despite the challenges.
Alloys in the 4XXX series are generally used as filler material for welding other aluminum alloys, including those from the 6XXX series. Their silicon content significantly lowers their melting point and allows them to pick up some of the alloying constituents of other heat-treatable alloys.
Finally, the remaining 1XXX, 3XXX, and 5XXX series alloys generally exhibit good to excellent weldability, though only the 5XXX series alloys are commonly used for applications requiring structural integrity.
6 Common Aluminum Alloys for Welding
The following table shows some of the most commonly welded aluminum alloys.
Alloy Designation | Advantages | Disadvantages | Common Applications |
---|---|---|---|
3003 | Very popular general-purpose alloy. Excellent formability and weldability | Not particularly strong. | Sheet metal work, stamping, fuel tanks, cooking utensils, electronics. |
5052 | Stronger than 3003. Good weldability and excellent corrosion resistance. | Not heat-treatable. | Pressure vessels, tanks, hydraulic tubing, appliances, marine applications. |
5083 | High weld efficiency and very high joint strength. Good corrosion resistance. | Not heat-treatable. | Drilling rigs, tanks and marine components, cryogenic applications. |
5454 | Moderate-to-high strength, excellent weldability. | Not recommended for cladding. | High-heat applications, such as trucking for hot asphalt road tankers and dump bodies, as well as some chemical storage vessels, such as for hydrogen peroxide. |
6061 | Good all-around alloy. | Not the best rated in any specific area. | Structural and welded assemblies, railroad cars, pipeline, aircraft, automotive parts. |
6063 | Medium strength and good corrosion resistance, weldability, and workability. | Not great machinability. | Extruded parts such as pipe railing, furniture, architectural, medical equipment. |
Conclusion: Can I Weld My Aluminum Product?
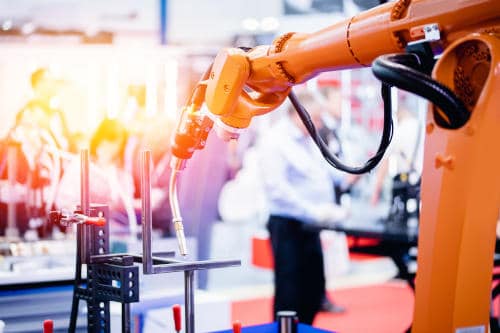
Robotic welder
If the formation process requires your aluminum product to be welded, there is a high probability you can do it! Aside from some exceptions, like many members of the 2XXX and 7XXX series, aluminum products can be joined by appropriate welding techniques.
In addition to manual welding, you can also consider robotic welding for your project. Robotic welding offers higher weld accuracy, consistency, and greater output. At Gabrian, we use robotic welding setups for some of our aluminum extrusion customers. You can also consider other joining methods for aluminum extrusions.
If you need assistance manufacturing your next aluminum product or require processing assistance, contact our team of service experts. You can also review our lines of rolled aluminum products and extruded aluminum products to see how we can meet your production needs.